某品牌手機生產(chǎn)公司,成立于1996年8月,是中外合資高新技術(shù)企業(yè),擁有員工13000余人,形成了以工業(yè)化、生產(chǎn)和直接分銷為核心的業(yè)務(wù)體系,已經(jīng)具備一秒鐘生產(chǎn)1.5部手機的生產(chǎn)能力,并入選中國企業(yè)500強、中國制造業(yè)企業(yè)500強并躋身中國通信器件和設(shè)備及零配件制造業(yè)企業(yè)前列。
隨著市場競爭的加劇,手機產(chǎn)品的生命周期變得越來越短,品種也越來越多。生產(chǎn)也隨之波動,呈現(xiàn)多品種、小批量、短周期等特點,許多生產(chǎn)企業(yè)的問題也暴露出來,某品牌手機生產(chǎn)公司也不例外,曾經(jīng)由于忽視產(chǎn)品品質(zhì)管理細節(jié)問題而出現(xiàn)過重大質(zhì)量問題:在2014年,因生產(chǎn)管理及品質(zhì)管理過程中的疏忽,包裝盒上的標簽漏打了一行字符導(dǎo)致出口的一批產(chǎn)品遭到客戶投訴,公司就付出了近百萬歐元的損失,公司的信譽也受到了巨大的影響。
因此某品牌手機生產(chǎn)公司為了適應(yīng)自身及客戶要求,以縮短交貨期、降低成本、提高質(zhì)量為目的,決定聘請天行健咨詢公司的資深顧問入廠指導(dǎo),引進精益六西格瑪管理思想來開發(fā)企業(yè)內(nèi)部潛力,加強科學(xué)管理科學(xué)管理方法對生產(chǎn)系統(tǒng)經(jīng)濟效益分析與研究,并提高經(jīng)濟效益,降低成本,提高品質(zhì),以增強某品牌手機生產(chǎn)公司的競爭優(yōu)勢,打造世界級手機制造旗艦企業(yè)。
1、提高人工生產(chǎn)率,從而降低單件的生產(chǎn)成本;
2、生產(chǎn)線平衡率達到95%,生產(chǎn)率達到105%;
3、提高員工的生產(chǎn)情緒低和工作效率;
4、服務(wù)水平由96%提升到98%;
5、成本下降10%、產(chǎn)能提高75%。
一、5S改善活動
某品牌手機生產(chǎn)公司5S改進以前員工對5S的要求不清楚,物料擺放不整齊,紙箱帶灰塵、紙屑,目視化管理標準不明確。很明顯在這樣的5S環(huán)境中工作,員工的生產(chǎn)情緒低落,工作效率不高,作業(yè)內(nèi)容不清晰,物流傳遞不流暢,作業(yè)空間浪費大,無形地增加了生產(chǎn)成本。
在公司里專門成立了5S管理小組,制作5S管理標準卡、獎懲條例以及5S控制程序,并在年終時將評選出年度5S優(yōu)秀團隊和5S明星,同時發(fā)放年度5S獎金作為公司對個人,集體在5S的積極推進管理中所做出的突出成績表示肯定和表揚。
通過積極推進5S的管理,時刻注意實施5S,對生產(chǎn)車間或辦公室,做到處處潔凈明亮,物品放置井然有序,標識、看板、通道暢通無阻,從而提高了企業(yè)的形象,獲得了客戶的信賴,成為企業(yè)無形的寶貴資產(chǎn)。公司把5S管理落到了實處,良好的5S表現(xiàn)己經(jīng)給到公司參觀的客戶留下了深刻的印象,獲得了客戶的認可,同時也增強了客戶對公司的品質(zhì)信賴,這也正是公司推進5S精益改進項目所帶來的直接和間接效益。
二、生產(chǎn)效率精益六西格瑪改善
為了改善按時交貨率(On Time Delivery)和全面提高公司的質(zhì)量水平以進一步滿足客戶短交貨期的需求,公司積極推行生產(chǎn)效率精益六西格瑪改善活動。
1、定義(Define)
經(jīng)過比較,我們選取生產(chǎn)線平衡較差、一次通過率(FPY)較低95%、產(chǎn)量適中的項目組裝線為改進對象。根據(jù)SEIHAN里的預(yù)測L項目的需求,而根據(jù)需求預(yù)測推算出來需要的人工時:需求*每班工作時間/每班產(chǎn)能。
該項目歷時3個月,由主管生產(chǎn)的副總裁(VP) Kanako發(fā)起,工藝流程部門的黑帶擔(dān)任項目經(jīng)理,生產(chǎn)線平衡率和生產(chǎn)率分別作為衡量線體靜態(tài)和動態(tài)特性的指標,要提高生產(chǎn)線生產(chǎn)效率就要從這兩個指標著手。其目標要使項目生產(chǎn)線平衡率達到95%,生產(chǎn)率達到105%。
2、測量(Measure)
確定了目標,就要開始搜集數(shù)據(jù),明確目前的狀態(tài)。L產(chǎn)品改進前的組裝生產(chǎn)線layout和各工位的作業(yè)時間,如圖1和表1所示。
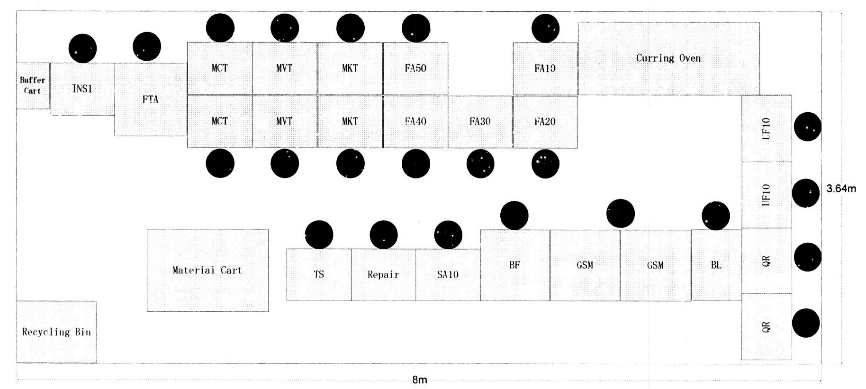
圖1
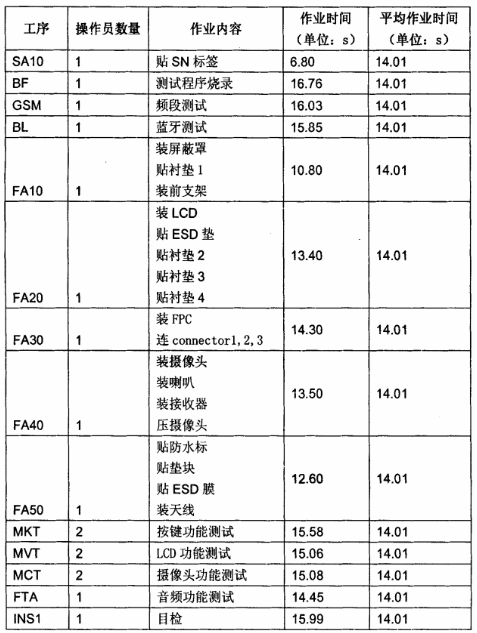
表1
3、分析(Analyze)
根據(jù)表1作出L產(chǎn)品改進前的各工位時間圖,如圖2所示。
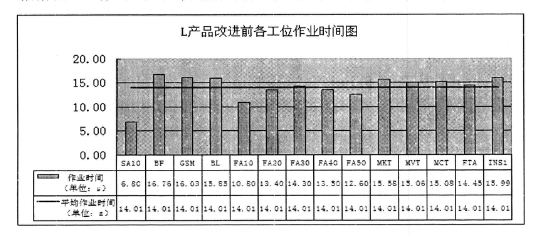
圖2
從圖2可以看出測試工位BF, GSM, BL用時很長,所有的測試站工時都高于平均時間,而SAW和FA10遠低于平均時間。測試工位時間長,肯定會出現(xiàn)人等機器的情況,可以考慮適當減少測試站的人員以減少人工等待的浪費,提高整條線的生產(chǎn)率。SAIO, FA10, FA50等組裝工位時間遠低于瓶頸時間,可以考慮重新組合裝配動作,平衡各站之間的差距,降低閑忙給的不平衡,減少線上在制品(WIP)的浪費和人工等待的浪費,提高人工生產(chǎn)率,從而降低單件的生產(chǎn)成本。
對于流水線而言,生產(chǎn)線效率的損失主要原因就是生產(chǎn)線平衡率低。根據(jù)生產(chǎn)數(shù)據(jù)的可以發(fā)現(xiàn)某品牌手機生產(chǎn)公司生產(chǎn)線平衡率普遍低于90%,有的項目的生產(chǎn)線平衡率甚至低于70%,對于整個公司來說這是很大的浪費,有很大的改進空間。所以公司設(shè)立生產(chǎn)率精益六西格瑪改進項目運用生產(chǎn)線平衡技術(shù)對生產(chǎn)線進行改善,提高生產(chǎn)效率。
4、改進(Improve)
分析出問題的關(guān)鍵,我們就要進行有針對性的改進,這樣才能有的放矢。然后,針對裝配工位的改進根據(jù)MODAPTS分析結(jié)果,在不影響裝配的前提下將裝配動作重組優(yōu)化平衡得到表2的作業(yè)時間分布。
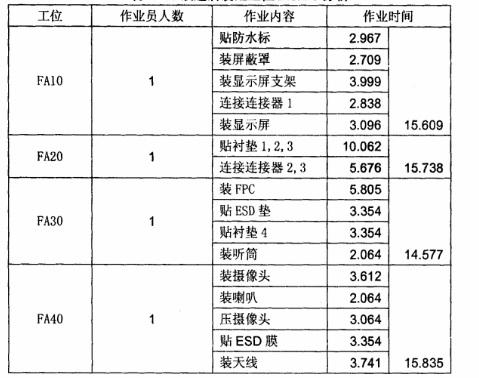
表2
一個月后,改進推廣至L產(chǎn)品10條生產(chǎn)線。L產(chǎn)品年產(chǎn)量200萬臺,每臺成本1000元,制造成本占總成本的,0%,所以L產(chǎn)品改進項目可以節(jié)省成本:200*5.46*12*10+3.1 *500*365*10=580w萬元。除去改進項目成本100萬,10條L產(chǎn)品線生產(chǎn)率改善精益六西格瑪項目可以每年為公司創(chuàng)造480萬元的效益。以此推廣至全公司的項目則每年可為公司創(chuàng)造數(shù)千萬的效益。
5、控制(Control)
生產(chǎn)線平衡率反映的是線體的靜態(tài)特顯,當生產(chǎn)的流程確定后其平衡率也就基本固化了,只有改進了生產(chǎn)流程時,才需要重新計算和測量平衡率。
生產(chǎn)率是用來評估生產(chǎn)過程中整體生產(chǎn)能力的指標之一,它包括了工程技術(shù)能力、設(shè)備維護能力和物料管理能力等對生產(chǎn)的影響,它反映的是線體的動態(tài)特性。圖3是L產(chǎn)品實施改進方案后的Line59生產(chǎn)率的追蹤報告。
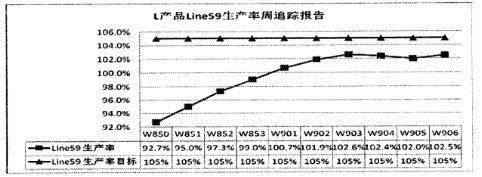
圖3
從圖3我們可以明顯地看到生產(chǎn)效率處于平穩(wěn)狀態(tài),說明我們的改進效果較好,狀況在控制中。從生產(chǎn)率的狀態(tài)曲線看,其他配合生產(chǎn)的部門的改善措施非常有效,使得生產(chǎn)率每周都有較大的提高,從W850周的92.7%提高到W903周的102.6%,已接近立項時提出的目標。
公司實施精益六西格瑪?shù)墓芾眢w系是一個非常艱苦的過程,但所取得的各方面的成績確實令人鼓舞。下表是公司實施精益六西格瑪項目改善后的主要業(yè)績指標。
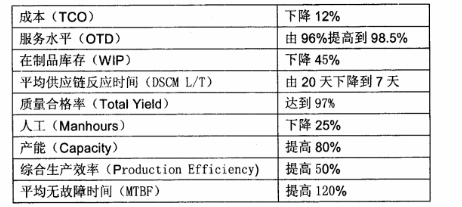
從上表中不難看出實施精益六西格瑪管理體系與傳統(tǒng)方式相比,項目結(jié)果的變化是顯著的。這些結(jié)果與設(shè)計的預(yù)期效果基本一致,說明公司的精益六西格瑪管理體系設(shè)計與實施是成功的。